Functional Safety. What Does Functional Safety Mean?
February 28, 2023
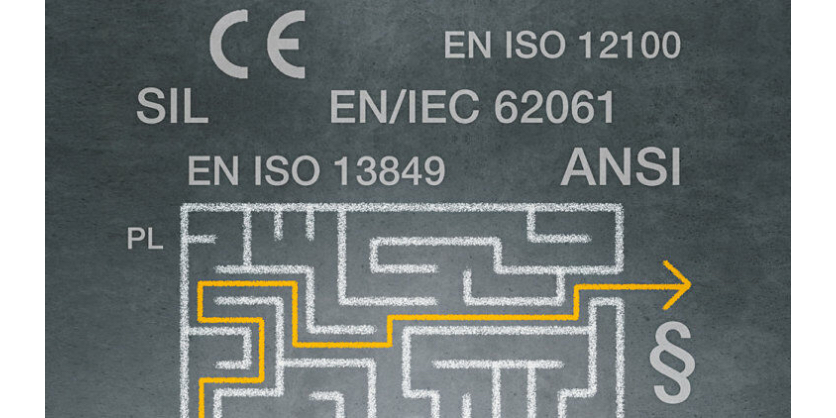
The causes of hazards and therefore the technical measures applied to avoid them can vary widely. As a result, different types of safety are differentiated, by the cause of potential hazards for example.
“Functional safety” is the term used when safety depends on the correct function of a control system.
Risk assessment plays a central role with regard to functional safety requirements. The steps you need to consider when assessing and reducing risk on machinery come from the standard EN ISO 12100. The evaluation and verification of safety functions are the prevail of the standards EN ISO 13849 and EN IEC 62061, provided the required safeguarding is dependent on a control system. The safety integrity requirements (PL, SIL) are derived from the risk estimation.
Presentation: Functional safety standards – Changes to ISO 13849-1 and IEC 62061
Functional safety standards are in a transition phase. IEC 62061 was republished in 2021, ISO 13849-1 is expected in the summer of 2022. How will this affect the design of safety-related control systems and compliance with the Machinery Directive? Find out more in the presentation!
Request the recording of our presentation for free
Functional safety standards – ISO 13849 and IEC 62061
Functional safety describes the part of a system’s safety that depends on the correct function of the safety-related control system. Generally speaking safety also depends on other risk-reducing measures, which are examined in accordance with EN ISO 12100. E-STOPs, safety gates, light curtains or speed monitoring are just some of the typical safety devices used to safeguard plant and machinery.
The rising level of complexity of plant and machinery means that programmable control systems are increasingly being used alongside conventional relays. Both ISO 13849 and IEC 62061 ensure compliance with international legislation, e.g. the Machinery Directive. Both standards are crucially important for plant and machine builders because many B and C standards refer directly to them.
Quo vadis “functional safety”?
In automation too, there is a trend towards digitalisation. The rising level of complexity means that configurable or programmable control systems are increasingly used to safeguard plant and machinery. When designing machine controllers, this question often arises in the course of the risk assessment: how do you select the required safety level for safety-related control functions?
Manufacturers must select and then combine the components in accordance with certain criteria. The risk estimation looks at the probability of a component failing to danger. The probabilities of failure of the various components must then be examined together. The required safety level is determined via graphs, which illustrate the severity of injury and the frequency or duration of exposure. The greater the risk, the higher the controller’s safety-related requirements.
Every safety function is examined in the process. For example, protection against unintended restart or shutting down via the E-STOP function in the case of danger, or even ensuring that the machine is still safe, should the controller fail.
Productivity must also be considered alongside demands for a safe machine. If not, the incentive to tamper with safety devices will increase.
The requirements of safety-related parts of machine control systems are defined in both ISO 13849 and IEC 62061.
Transition periods and harmonisation
Publication of ISO 13849-1 was originally planned for 2021 and was postponed to 2022. It is far from clear when it will be harmonised into the EU standard EN ISO 13849-1, whether there will be a transition period for publication of the standard in the Official Journal and, if so, how long this might be.
The process of harmonising IEC 62061 to EN IEC 62061lasted a year. As soon as an international IEC or ISO standard is published as an EU standard in the Official Journal of the European Union, presumption of conformity applies. That means that a manufacturer who abides by the specifications of the standard can assume that they comply with the health and safety requirements of the Machinery Directive and so, as part of the conformity assessment with the declaration of conformity, can affix the CE mark to their machine.
The ratified, international standards can be applied as soon as they have been published on the IEC and ISO websites. However, it is advisable to deal with the expected development at an early stage.
Functional safety at a glance
The aim of functional safety is always to protect humans and machines from hazards. In Europe, the relevant functional safety standards in the engineering sector are listed in the Machinery Directive. Download our “Functional safety” poster now and discover at a glance the procedure for risk assessment and risk reduction in accordance with EN ISO 12100. You can draw on two important standards, derived from this A-standard:
- EN ISO 13849-1: Applicable for electrical/electronic/programmable electronic/hydraulic/pneumatic/mechanical systems
- EN IEC 62061: Applicable for electrical/electronic/programmable electronic systems
Important parameters for the reliability of safety-related functions are the safety integrity level (SIL) and performance level (PL).
More Information
Download the functional safety poster
Related Service
Machinery Safety Evaluation from PILZ
The Machinery Safety Evaluation provides a comprehensive overview of the safety and conformity status of the machinery tested under the scope of this evaluation. You also receive a list of measures or check list to quickly derive the measures needed to optimise safety and compliance with the applicable laws, standards and directives.