The ‘Next Normal’ for Manufacturing: Embracing Operational Transformation
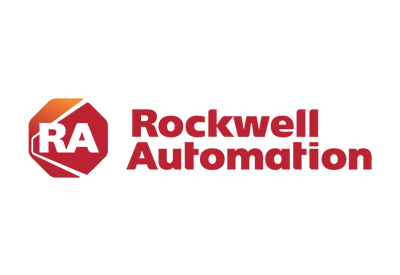
July 27, 2020
Jan Burian, Research Director, IDC Manufacturing Insights
In the past few months, IDC has spent a great deal of time talking with manufacturers in our community to understand how they are looking at the time ahead of us. We classify these inititives into three main waves.
First of all, we are looking at some initiatives that we see having a very short-term focus, which are essentially based around planning the reaction: learning how to manage contact tracing, supplier risk assessment, cash-flow modelling and remote working.
But they know that after these few months where everything has been frozen, a recession is impending. Actually, we expect a lot of market disruptions and a very bumpy road ahead.
Therefore, companies plan to adapt to these circumnstances by raising their operational agility and their demand-sensing capability. Most “second wave” initiatives cover these two aspects: improved S&OP; production scheduling, operational instrumentation and analytics.
After that long valley of disruption, economic recovery will eventually emerge, but the other side of the “U” will be different. We are talking about a “next normal”, and companies are already planning their transformation journey.
New Ways of Working
For example, there are a number of initiatives that pertain to enabling new ways of working. As we see from the multiple announcements companies have released, they are already working hard in re-assessing their processes and making them fit for purpose for a socially distanced world.
Processes in factories and offices have to be run in completely different ways, and technology can also help by enabling operations to be more autonomous and remotely controlled, thus reducing the need for people to record stats and monitor machines while increasing the real-time visibility over operational status.
Even more interesting, companies are experimenting with new business models. This entails collaborating with companies that come from every sector by creating ecosystems of business-model innovation. We have all seen the initiatives that companies have put together in order to rapidly ramp up the production of medical devices and PPEs, whether it is the collaboration of Volkswagen and Airbus, Ford with GE Healthcare or 3M, General Motors and Ventec Life Systems, ŠKODA AUTO, and Czech Technical University, or the UK “Ventilator Challenge”.
Now that the psychological barrier from collaboration has been brought down, we see companies are thinking about potentially carrying these concepts forward to support their processes. This can be quite adaptable.
What many of the above examples have in common is the fact that companies have been able to ramp up production for most of these completely new products in a very short time. In most cases, there was a company that provided the necessary production capacity, another their supply chain, transport capacity, knowledge of product design, or the availability of 3D printers.
Digital Transformation Now and in the Future
This is the future of enterprise, fueled by digital transformation.
As such, it is not a surprise that, according to the most recent IDC research, manufacturers report a focus around technology as the main driver for operational improvement – higher than cost reduction and quality, for example.
Furthermore, smart manufacturing ranks as the top area of focus for manufacturers worldwide when it comes to next-gen investments – more than 30% are placing it as a key priority for the year, and a similar share for the next 24 months.
In fact, as plants are now seen as supply-chain bottlenecks, they are becoming the primary targets for new investments. Companies realise that business process reinvention and business model transformation must be enabled by solid factory capabilities and a “back to basics” attitude that sees the factory as a key contributor to companies’ value proposition.
It is also very telling that manufacturing execution systems rank just after smart manufacturing in terms of investment priority. While not a new technology, these systems are still as relevant as ever being now evidently seen as the key enabler for business process improvement and the ideal complement to IIoT and smart factories investments.
Leading the Next Normal
And here we are getting to a conclusion that has already been confirmed in our previous research on the behavior of manufacturing companies at the global level. Given that we expect a significant slowdown in the economy, now is the best time to start thinking about what to do differently in the future.
Traditional cost-saving approaches are only effective to a certain extent and will certainly not bring anything miraculously new. It will allow the company to survive at best but will stop much-needed investment and new process improvement in the future. The winners in the “next normal”, will be those who can build a competitive advantage on their flexibility.