University of Virginia Maintenance Team Relies on ABB to Keep Campus Running
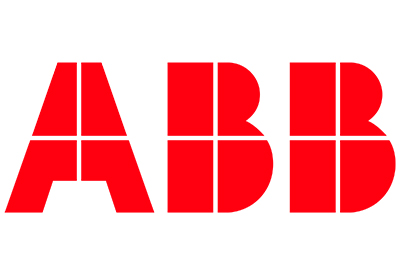
June 4, 2020
Keeping a university’s buildings up and running during regular times is no small feat, much less during an unforeseen campus shutdown. When the Covid19 pandemic closed the University of Virginia in spring 2020, a maintenance team responsible for the McCormick zone of campus relied on over sixty-five ABB Ability Smart Sensors for mechanical products to keep their critical lab environments stable and equipment performing. The ability to know when there was a problem – without physically being there – also allowed the University maintenance team to operate safely during this unprecedented time.
The path to smart sensors
The University of Virginia McCormick maintenance team is responsible for ensuring that approximately ten buildings on campus maintain comfortable temperatures for students and faculty at the University of Virginia, and that each research laboratory in their zone maintains stable environment needed for controlled experiments. Past maintenance practices required nearly daily work on air handling equipment, generally a belt driven fan, supported by mounted pillow block bearings on both sides of the fan. Some of the fan assembly is built inside the box so it is impossible to access while running. With the running of the fan, it is also difficult to hear, much less get vibration or temperature readings without shutting down the unit and compromising the environments in the buildings.
In the fall of 2019, the team learned about the ABB Ability Smart Sensors for mechanical products. The ABB Ability Smart Sensor for mechanical products is a monitoring solution that provides an overall health indication of your equipment to let you know when maintenance is needed. The sensor gives warnings on decreasing health status, which allows you to plan maintenance before there is a problem and the system is down. The ability to monitor equipment remotely allows maintenance teams and other relevant personnel to safely get a health check without touching equipment.
The mechanical smart sensor had not been on the market long, but without similar technology on the market with the features offered in the ABB sensor, several were put on the bearings for a test. The sensors proved successful – letting the maintenance team know how equipment was holding up and alerting them to problems prior to an unplanned shutdown. Due to the success, sensors were added to bearings on additional HVAC units.
Changing the maintenance landscape
As sensors were added to critical air handling unit bearings across the facility, the team encountered warnings on equipment that they were not aware needed maintenance or replacement. After each correction, the team added a sensor to compare conditions prior to repair. The absence of warnings and indication that the vibration levels were nearly perfect proved that repairs had been done properly.
The sensors have also changed how the team schedules maintenance and maintains spare parts inventory. Based on sensor data, the team knows what truly needs attention each day, rather than relying solely on a prescribed maintenance schedule. This also reduces inventory because the warnings give them plenty of time to buy needed parts and schedule maintenance without unplanned downtime. The sensors allow the team to better manage time and budget, ensuring all the labs are stable.
And right now, they are allowing the team to safely keep the university running without physically being there.