Rethink What’s Possible With Your HMI
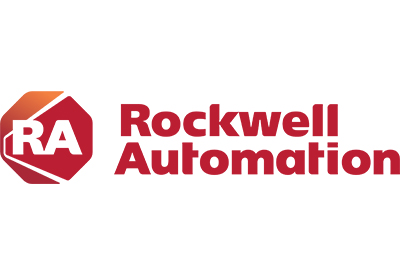
May 19, 2020
By Susan Burtch, Visualization Software Marketing Manager, Rockwell Automation
You may view your HMI software as the tool that puts production data in front of workers at terminals. But the truth is, modern HMI software does a lot of work “behind the glass” that, if leveraged, can help improve how your operations run.
From the ability to pull up production status anytime and anywhere, to the ability to integrate with a wide range of plant-floor systems, today’s HMI software can do things you may not have imagined possible just 10 years ago.
Here’s a look at three key ways a modern HMI can transform your operations.
Access Insights in New Ways
A modern HMI doesn’t just give workers access to information. It gives them access to information in the time and place that they need to make decisions.
How? By extending displays beyond operator terminals with new technologies like mobile devices, thin clients, or mixed-reality headsets – giving workers faster, more convenient access to information in their moments of need.
When technicians can access HMI displays on mobile devices, for example, they can see and react to alarms remotely to more quickly address production issues. And by delivering displays to thin clients, your business can reduce maintenance, save money and enhance security compared to using PCs.
Create More Familiar Operations
As workers access more production information on a wider range of devices, it’s important that displays be consistent, so workers always know what they’re looking at. A modern HMI allows you to deliver a standardized look and feel across operator terminals, PCs and tablets to create a familiar operating environment.
A modern HMI also allows you to store and reuse device faceplates and other objects in a library. This can help make sure workers see elements consistently as they move from machine to machine, line to line, or even plant to plant.
Get More From Your Data
A modern HMI can connect to your other industrial systems to give workers deeper visibility into operations and improve your overall performance.
For example, the software can integrate with your production systems to give workers access to not only real-time controller information, but also information stored in devices on the plant floor. This can help workers better manage quality, optimize equipment performance and more.
Similarly, the software can connect to a historian to help workers more easily analyze complex process data over long periods of time. Historical process data can be combined with operator actions, system alarms, and even production system events to provide data to the operator with the context that makes analysis easier.
A modern HMI can also work in tandem with asset-management software to backup and recover your HMI applications – in addition to your controller and other device configurations. In the event of a catastrophe or downed machine, engineers can then simply reload the applications instead of rebuilding them.