Mitsubishi Electric: iQ-R Motion CPUs for Advanced Applications R16MTCPU, R32MTCPU, R64MTCPU
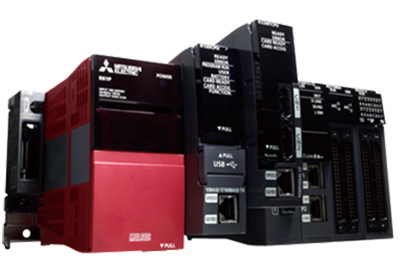
October 28, 2019
The R16MTCPU, R32MTCPU, and R64MTCPU motion CPUs are dedicated motion control processors designed to execute advanced synchronous control functions and high speed registration, independent of PLC scan time, for maximum performance. The dedicated Motion SFC language and graphical mechanical editor tool are optimized for the toughest synchronous motion applications in the world, including high speed printing presses and large converting lines.
Key Benefits
-
SSCNET III/H high speed motion network – Provides high speed noise-immune communications, reduced wiring, and excellent troubleshooting, diagnostics, and maintenance functions
-
16, 32, and 64 axis motion CPUs – Scalable solution with up to 3 motion CPUs per system, for a total of 192 axes
-
Advanced synchronous control – High performance motion functions including camming, gearing, registration, point tables, interpolation, and indexing
-
One‑Touch Auto‑Tuning™, and Advanced Vibration Suppression Control II™ – Industry leading servo and motion control performance when combined with the MR-J4 series servo drives and motors
-
Ultra‑high speed registration – Improves finished product quality by allowing the equipment to automatically adjust for variations in the size and position of incoming product and ensuring perfect color- to-color print registration
-
Capable of precision tension control without dancers or load cells – Reduced hardware complexity with improved tension regulation
Dedicated Motion Processor
The motion program operates independent of PLC scan time for maximum performance, regardless of PLC CPU load. Motion SFC language minimizes unnecessary code execution for even faster processing and reduced latency.
Multiple Programming Languages
Multiple IEC 61131 programming languages are supported in the PLC. The Motion SFC language, which is specifically designed for high speed motion applications, provides an intuitive flow chart programming experience for the motion CPU. This flexibility allows the user to program in the most efficient manner for their application.
Easy System Synchronization
Servo synchronization is easy with the graphical mechanical editor. Simply drag and drop mechanical devices on the screen and set related parameters such as speed change gear ratio or clutch control type to drastically reduce configuration time of synchronous systems.
Optimum Performance With Minimum Effort
MR-J4 servo drives feature One-Touch Auto-Tuning and Advanced Vibration Suppression Control II. These industry leading features ensure that the commands from the motion controller are accurately reflected at the product regardless of the condition of the mechanical system.
Advanced Synchronous Control
Applications requiring camming and gearing are easily implemented by simple parameter settings. Control via software rather than mechanical components reduces maintenance and commissioning time, and increases machine flexibility.