B&R Automation: Digital twin
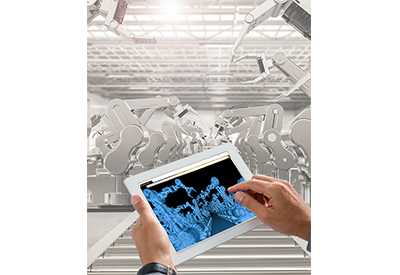
September 23, 2019
B&R’s two new software packages greatly simplify model-based machine development. The B&R industrialPhysics package allows developers to quickly and efficiently generate a digital twin for developing and testing machine software. B&R MapleSim enables the detailed modeling of physical processes and the calculation of force and torque values.
Highlights
- Digital twins for accelerated software development
- Adopts CAD model properties
- Detailed drive simulation in Automation Studio
- Real-time 3D-HMI application in B&R Scene Viewer
Digital twins are the key to efficiency when it comes to software development and the virtual commissioning of a machine. B&R industrialPhysics is based on the industrialPhysics software from one of the leading manufacturers of 3D simulation software. It is specially designed for Automation Studio and B&R target systems. With B&R industrialPhysics, the physical behavior of the machine can be displayed in real-time. This is useful for collisions and material flow, for example.
Using a digital twin allows software and hardware development to run in parallel. Bottlenecks and optimization potential are identified at a very early stage. Any configurations that the application developer makes on the digital twin can be transferred directly to the real machine. This plays a key role in maintaining speed and continuity in the machine development process.
Importing CAD data
B&R industrialPhysics uses CAD data to create the digital twin. The data is imported in STEP format, which means that the most important properties of the CAD design, such as mass and density, can still be used. In addition, B&R industrialPhysics provides the individual mechanical components with additional properties, as well as the degree of freedom of the components and the controller interface. The developer can immediately start the virtual model on the PC and connect to the controller in a software- or hardware-in-the-loop configuration.
Dynamic machine model
The B&R MapleSim software package is based on Maplesoft’s modeling tool. MapleSim creates a highly accurate, dynamic representation of the machine based on CAD data in STEP format. Since all forces and torques are accurately represented, the model can be used as a digital twin for component sizing. B&R MapleSim provides a simple and intuitive approach for modeling mechanical systems, but that’s not all. It also provides a selection of basic components in the areas of electrical engineering, hydraulics and thermodynamics that facilitate the modeling of physical interactions.
B&R MapleSim provides two export functions, known as Toolboxes, for efficient use of the digital twin in the development process. With one, simulation data can be exported for the optimal sizing of servo drives, motors and gears for tools such as ServoSoft. Alternatively, the model built in MapleSim can be exported as an FMI file. This allows it to be used as a simulation model in Automation Studio. Control parameters, temperature behavior of the drive and machine load are simulated right in the development environment. B&R Scene Viewer visualizes the digital twin in 3D and in real time.
Automatic code generation
The two new products join Automation Studio Target for Simulink to complete the versatile modeling and simulation options in the B&R system. The software enables automatic code generation from MATLAB/Simulink for B&R target systems. The developer can create a model in Simulink, and then, at the click of a mouse, generate high-quality program code to be run on the B&R controller – including sophisticated diagnostic options provided by Simulink.