Why you should always supplement your safety light curtain with stop time measurement
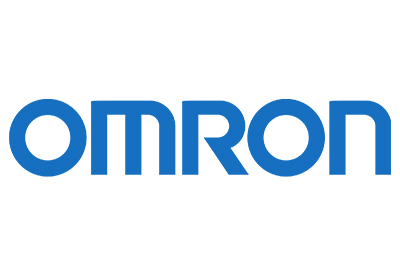
August 15, 2019
A safety light curtain can help avoid serious accidents on the factory floor by ensuring that a potentially hazardous machine ceases operation before a person enters the hazard zone. However, this is only the case if the light curtain has been set up at a sufficient distance relative to the time it takes for the machine to stop.
According to ANSI B11.19 – 2010 in Annex D, if safeguarding devices do not physically prevent individuals from reaching into a danger zone, they must be located far enough away from the potentially hazardous motion of the machinery so that this motion can be prevented, completed or stopped before the individual can be harmed.
Safety light curtains don’t physically prevent access to danger zones
Safety light curtains are a prime example of a safeguarding device that doesn’t physically prevent entrance into a danger zone. Rather, a light curtain is simply a presence-sensing device that can trigger a response from the machine. What if a person were to move past the light curtain so quickly that he or she came into contact with machinery that was still in motion?
For this reason, a stop time measurement is essential for ensuring that safeguarding devices like light curtains and other presence-sensing devices have been mounted at the minimum allowable safe distance to properly protect operators. The stop time measurement service determines the amount of time it takes for a machine to stop once it receives the signal to do so.
In addition to safety light curtains, other safeguarding devices requiring a minimum safety distance include but are not limited to:
- Interlocked guards (non-locking)
- Two-hand control devices
- Two-hand trip devices
- Single control safeguarding devices
- Electro-optical presence-sensing devices
- Radiofrequency (RF) presence-sensing devices
- Safety mat devices
- Safety edge devices
How does stop time measurement enter into safety distance calculations?
In the United States, there are two methods for calculating the minimum allowable mounting distance (“safety distance”) for a safety device: the OSHA (Occupational Safety and Health Administration) formula and the ANSI (American National Standards Institute) formula. The ANSI formula takes more factors into account and provides a more comprehensive result.
Factors that safety distance calculations consider include the individual’s approach speed, the light curtain’s response time, and the machine’s stop time. Calculations vary according to whether they are considering the individual’s whole body vs. just a hand or an arm. In the latter case, the light curtain’s detection capability must also be taken into account.
Some machines have a fairly lengthy stop time – also known as a “coast-down time” – due to fast-moving processes that could cause significant damage if stopped quickly. In these cases, simple presence-sensing devices may be insufficient. Instead, a manufacturer might want to consider a more robust safeguarding solution, such as guard-locking interlock switches.
By ensuring that your safety devices are mounted at the proper distance, you can protect the value and safety of your initial investment in a comprehensive safety solution. In addition, a stop time measurement service will help you maintain records for OSHA and ANSI compliance.