Rockwell Automation: How to Reduce Lead Time with Smarter Machine Engineering
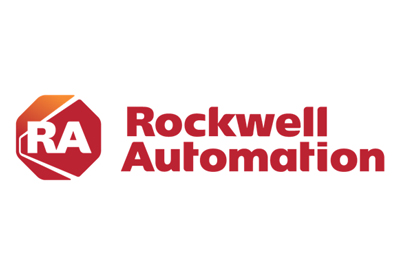
June 19, 2019
By Steve Mulder, Rockwell Automation and Eric Langen, AFA Systems
How fast can we get it?
It’s the number one question that comes after presenting a new packaging solution you’ve developed for a customer. And it’s one of the top challenges facing machine builders today.
So, how do you get from concept to machine faster in an environment that demands customization, flexibility and speed? That’s what packaging machine builders face every day. And one answer is to simplify.
Let’s start at the top. Providing custom machines and equipment to solve a customer’s unique challenges is how many custom machine builders have made their name.
That’s especially important today when packaging must be innovative, multi-functional and stand out on the shelf, all requiring new engineering and never before tested concepts. And whether or not a packaging OEM can meet the novel specifications cost-effectively is directly related to their approach to machine design.
One company is tackling this challenge head on. AFA Systems, based out of Ontario, Canada, is a global leader in engineered packaging automation systems. Not unlike other custom machine builders, engineering is at a premium. Streamlining any part of the design and build process can be invaluable in solving how to reduce lead time. AFA has found efficiencies in embracing a single control platform to integrate complete line, cell and robot control programming, commissioning and maintenance.
Programming in Operational Efficiency
Adopting a single platform allows machine builders to create modular components and standardize on assemblies to get machines into production quicker. It also allows OEMs to take full ownership of their solution, including service and support.
The alternative is the minefield of trying to tie disparate systems together to create one final solution. Multiple suppliers, systems and protocols add unnecessary time, resources and long-term support needs that can strain your technical resources. Leveraging preconfigured solutions and familiarity can save as much as 20 percent on engineering time on a portion of a project. It also allows for faster reconfiguration down the road. And that all adds up.
AFA Systems is an early adopter when it comes to standardizing a single control solution that includes robotics. The company was able to simplify training, operation and maintenance for its customers by using just one control platform for all machine operations. Additionally, machine performance improves with better coordination between the robot and other motion.
The company found that by hiring programmers who are familiar with the same system, in this instance a Rockwell Automation platform, all technology originates from and stays in house. That means AFA Systems can troubleshoot their own equipment. This is a welcome change after experiencing some challenges when coordinating with third-party suppliers to service and troubleshoot their customers as intimately and quickly as they’d like.
Industrial automation is changing at a pace we haven’t seen in the past. And it can be a full-time job just to keep up. The costs associated with training and support for multiple brands can cancel out other hard earned efficiencies you’ve built into your process.
“It’s hard enough to keep up-to-date with one ecosystem of control products. So we made the choice to work with one platform,” said David Langen, co-president at AFA Systems. “Beyond saving on training, we can leverage products so much better because we’re specialized in the control architecture.”
Taking this off your plate and relying on an automation partner makes the hurdle of learning a proprietary robotic control language disappear.
“In our case, as long as we’re keeping up with Rockwell Automation technology, we’re also keeping up with robotics technology, because they’re doing that for us,” added David.
From Reducing Lead Time to Improving Relationships
In the process of solving how to reduce lead time and development costs for your own operation, you’re also reducing lifecycle costs and eliminating an interface point for the customer.
Easy to access, long-term support is important in an industry where customers are always reconfiguring packaging to suit consumer and marketing needs.
David explains, “At AFA Systems, we have a machine with integrated robotics on our floor for modification that we built 10 years ago. Because the programming initiated in-house, our engineers can help the customer continue to get the most out of their investment, from major redeployments to everyday troubleshooting.”
Operational Efficiency is Your Future
The operational decisions you make today and how you utilize your limited resources can significantly impact your organization’s future growth. And as industrial robots are increasingly relied on to perform more tasks, the savings gained from standardizing on a control platform will only grow as well.
OEMs that can find the right balance between machine customization and streamlined engineering will grow their business and gain market share through innovation and efficiency.
This blog was co-authored by Eric Langen, Sales and Marketing Manager, AFA Systems.