Stay Resilient Against Resonance with AC Drives Adaptive Tuning
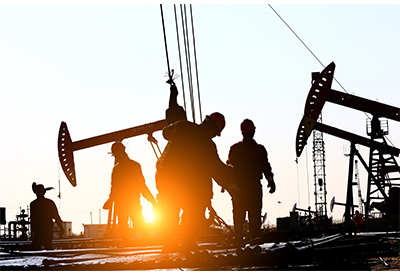
April 16, 2019
By: Brian Fast, Senior Project Manager, Rockwell Automation
It can be a scary moment on the plant floor: A machine starts shrieking and shaking so violently, you think it might break.
This incident can result from mechanical resonances caused by a load attached to a motor. Many design factors attribute to the resonances such as physical size, material selection, and instillation procedures. And while workers can usually make a control adjustment to resume production, resonance issues have lasting consequences on your machines and your business.
In the past, the typical adjustment to resolve the resonance degraded performance or resulted in wasted energy.
New low-voltage AC drives with adaptive tuning can help you better combat resonance issues, so you perform better and spend less. During production, the drive identifies the problem and applies the correct solution – resulting in a higher performing machine that accounts for machine variations.
Think of these smart drives like guards. They keep a vigilant watch of your application for undesirable resonance. If they see something wrong, they can sound the alarm or even attack the issue on their own. And by helping you win the war against resonance, the drives can help you stay running longer while reducing your repair and energy costs.
Our PowerFlex 755T drives are designed to provide harmonic mitigation, regeneration, and common bus solutions that help reduce energy costs, add flexibility, and increase productivity.
Protect the Potential of Your Machines
Resonances result from design decisions which may or may not be modeled by the designer. Known design decisions include the load shape, material selection, dimensions and physical size. Unknown design decisions include tolerances, assembly processes and motor characteristics. The resonances may change over time because of normal machine wear and tear. This can include applications which use shaft extensions or large loads like winders.
The previous approach to resolving resonances are to detune the regulator gains. This can stop a machine from shrieking and shaking, but it can also decrease the machine’s performance. Over time, this hurts your throughput and slows your reaction time to issues.
An AC drive with adaptive tuning uses advanced analytics to continually look for and detect different types of resonance. The drive can alert operators of issues in real time, so they can quickly act. In more advanced configurations, the drive can use special filters to mitigate resonance instead of detuning the controller.
This ability to autocorrect issues allows you to maintain the high level of performance that you expect. Based on load characteristics, we’ve seen two- to four-times-higher performance when using adaptive tuning.
Also, AC drives with adaptive tuning allow you to monitor resonance over time and schedule repairs, if conditions warrant. This can help you work smarter by addressing issues proactively and during scheduled maintenance windows, rather than abruptly in the middle of production.
To learn more about drives with adaptive tuning, check out the new PowerFlex® 755T AC drives with TotalFORCE®technology.