Value creation 4.0 with Rittal at the Hanover Trade Fair 2019
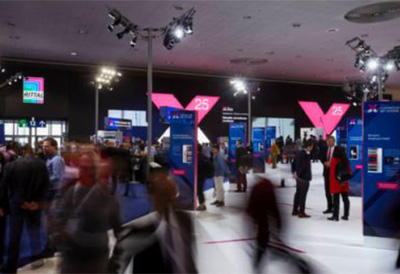
April 11, 2019
At the Hanover trade fair (Hannover Messe) 2019, Rittal presented the benefits generated by new and enhanced system products, digital processes and an appropriate infrastructure. One of the highlights was the unveiling of a new generation of compact and small enclosures.
Industrial intelligence requires seamless connections between people, machines and data. At its 1,550 m² stand at the Hanover trade fair Rittal put a spotlight the opportunities created by end-to-end digital integration: beginning at an Industry 4.0 marketplace, visitors can discover through dialogue how Rittal is interpreting this year’s trade show theme, “Integrated Industry – Industrial Intelligence”, to the benefit of its customers. “Our digitalised product portfolio and direct interaction with visitors drawn from all industries are the ideal basis for in-depth discussion of how to best achieve process efficiency,” states Uwe Scharf, Managing Director, Business Units and Marketing. Rittal technologies are deployed in more than 90 per cent of all industries worldwide.
Premiere: new compact and small enclosures designed for the age of Industry 4.0
The Hanover trade fair also witnessed the unveiling of entirely new products: “We have understood the new imperatives of digitalised industry, and developed a new generation of compact and small enclosures in response. Our core products are being entirely redesigned, to be fit for Industry 4.0,” explains Uwe Scharf. The launch of the new small and compact enclosures marks the digital transformation of a standardised product that has been made by Rittal for more than 50 years: 35 million units of the AE have been manufactured, making it the most popular compact enclosure in the world. It is regarded as the original, and the first-ever mass-produced industrial enclosure. Now, Rittal has addressed the evolving needs posed by the digital era, and created a completely revamped and rethought system product. Customers benefit from new functions that streamline and accelerate their value-creation processes, while improving flexibility and reliability.
A new production plant geared to Industry 4.0
In Haiger, in the German state of Hesse, Rittal has built an entirely new facility for production of the latest compact enclosures. The single largest investment in the company’s history, totalling 250 million euros, has established the world’s most advanced factory for compact and small enclosures, in line with Industry 4.0 principles. The highly automated facility will be integral to seamless order management and fulfilment, ensuring the continuous availability of standard products and corresponding accessories. Visitors to the Rittal stand will discover just how connected, digital manufacturing processes work, and how they can leverage them for their own business success.
Helping panel builders and switchgear manufacturers master the challenges of Industry 4.0
Rittal again demonstrated that it goes beyond individual products, and is committed to addressing the entire value chain in the manufacture of control systems and switchgear. It is actively supporting this key industry in its efforts to drive forward digitalisation, standardisation and automation. The companies presented integrated solutions all along the value chain: from the provision of digital article data and product configurators to the engineering and work preparation process in which the enclosure’s digital twin is created, right through to digitally connected production.
Intelligent power distribution
Rittal also unveiled recent developments in power distribution, including high energy efficiency, the high availability of quality data, and ease of configuration by means of recently released Rittal Power Engineering software.
Tangible customer benefits through digital products and services
Industrial intelligence makes it possible to harness data and algorithms to monitor and manage the operation of systems, and to reliably predict faults or component failures: in manufacturing, in electricity grids, and in logistics. Rittal will also be showing customers the advantages of intelligent data analytics, i.e. in conjunction with its IIoT-ready products. This entails integrating active solutions such as cooling units, chillers and machines with information management tools via sensors and IoT or IIoT interfaces – residing on Rittal platforms such as EPLAN eView and RiZone, or on standard platforms such as Siemens MindSphere.
Intelligent edge data centres
Industry 4.0 and smart industry call for low latency in conjunction with high reliability and security. Rittal supplies the corresponding infrastructure. Five edge data centres will be on display in typical use cases. The highlight is the intelligent edge data centre (IEDC), developed in an alliance with Atos and Siemens.
The IEDC captures all relevant data within Industry 4.0 production facilities. At the Hanover trade fair, Rittal underlined its strengths within realistic scenarios based on data generated by Blue e+ cooling units. The Siemens MindSphere platform is the basis for data collection and the corresponding services. Visitors also gained insights into potential benefits via demonstration use cases, such as the visualisation of Rittal production processes in Rittershausen via the MindSphere app, and data management in the cloud by means of iNNOVO in combination with MindSphere.
Value chain engineering
At their dedicated stand H30 in hall 6, Rittal subsidiaries Eplan and Cideon showed how tailor-made engineering solutions can effectively support customers’ digital transformation strategies. The focus was on the Efficiency Lab. The Eplan and Cideon experts will work with visitors to model current and target engineering processes, and to perform gap analysis as the basis for systematic digitalisation.
Go HERE for more information